FDA warns manufactures of infant ‘drugs’ and bread products about violations
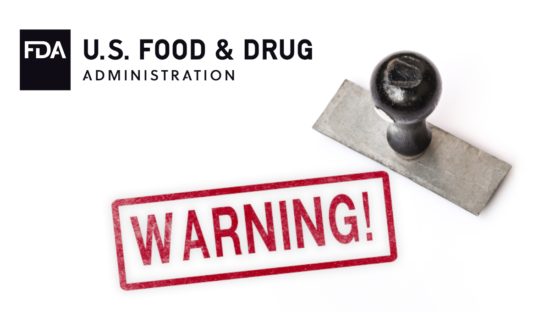
As part of its enforcement activities, the Food and Drug Administration sends warning letters to entities under its jurisdiction. Some letters are not posted for public view until weeks or months after they are sent. Business owners have 15 days to respond to FDA warning letters. Warning letters often are not issued until a company has been given months to years to correct problems. The FDA frequently redacts portions of warning letters to protect companies.
M.O.M. Enterprises LLC
1001 Canal Boulevard, Suite C
Richmond, CA 94804
The U.S. Food and Drug Administration (FDA) conducted an inspection of your dietary supplement facility located at 1001 Canal Boulevard, Suite C, Richmond, CA, from August 19 through Sept. 27, 2024. Based on inspectional findings and a review of your product labels collected during the inspection, as well as a review of your firm’s website, www.mommysbliss.com, we identified significant violations of the Federal Food, Drug, and Cosmetic Act (the Act) and applicable regulations.
At the conclusion of the inspection on Sept. 27, 2024, our investigator provided your firm with a Form FDA 483, Inspectional Observations (FDA 483). We acknowledge receipt of your responses dated Oct. 17 and Nov. 22, 2024, and January 10, 2025; we address your responses below.
Adulterated Dietary Supplements
The inspection of your facility from Aug. 19 through Sept. 27, 2024, identified serious violations of FDA’s regulations for current Good Manufacturing, Packaging, Labeling, or Holding Operations for Dietary Supplements, under Title 21 of the Code of Federal Regulations, Part 111 (21 CFR 111). These violations cause your dietary supplement products Gripe Water Original, Gripe Water Night Time, Kids Cough Syrup & Mucus + Immunity Support, and Kids Cough Syrup & Mucus Night Time (including such product in the Day + Night Combo Packs) to be adulterated within the meaning of section 402(g)(1) of the Federal Food, Drug, and Cosmetic Act (the Act) [21 U.S.C. 342(g)(1)] because they have been prepared, packed, or held under conditions that do not meet cGMP requirements for dietary supplements.
Your significant violations of the cGMP requirements are as follows:
1. You failed to extend the review and investigation of a product complaint to all relevant batches and records, as required by 21 CFR 111.560(c).
You initiated a market withdrawal of eight lots of Kids Cough Syrup & Mucus + ImmunitySupport, Kids Cough Syrup & Mucus Night Time, Baby Cough Syrup & Mucus + ImmunitySupport, and Baby Cough Syrup & Mucus Nighttime, including those in the Day + Night Combo Packs, on April 19, 2023, after your contract manufacturer notified you of early spoilage in these products. You reformulated the product to include the addition of glycerin to lower the water activity and also lowered the pH of the products, but your investigation did not extend to all relevant batches and records. After your firm initiated the market withdrawal, you received at least (redacted) complaints from September 2023 through May 2024, in which complainants described bulging bottles of product and product where the lids popped off, including (redacted) complaints for Kids Cough Syrup & Mucus Night Time, Lot Number (redacted), EXP 03/25, which lot was not included in your market withdrawal. For example, complaint #(redacted), received on Dec. 1, 2023, for Kids Cough Syrup & Mucus Night Time, lot number (redacted), stated that “(redacted)” and described “(edactedr).” Relating to this complaint, your “(redacted)” states, “(redacted). The product has since reformulated the product [sic].” Your investigation, however, does not explain how such reformulation would have addressed the issue relating to bulging product bottles and product packaging that popped open, nor did it address the concerns relating to this specific lot that had not been withdrawn from the market.
In your Oct. 17, 2024, response, you indicate the mold complaints were not new problems and were part of a previously investigated issue. However, your response does not explain how you determined that the issues were connected to complaints you received subsequent to the market withdrawal. You did not conduct additional investigations of these complaints to determine whether additional lots of product were affected by the known spoilage issue to determine if additional corrective actions were needed, even though your complaint records correlate these complaints to your market withdrawal.
2. You failed to follow written procedures for the requirements to review and investigate all product complaints, as required by 21 CFR 111.553. Your “(redacted)” procedure, revision date March 14, 2019, SOP #(redacted), and your “(redacted)” procedure, effective date July 1, 2022, QA-1009, both require your quality control manager to review complaints to determine whether the complaint involves a possible failure of a dietary supplement to meet any of its specifications, and to review and approve decisions to investigate complaints and any findings and follow up actions, in accordance with 21 CFR 111.560(a) and 21 CFR 111.560(b). However, a review of complaints you received from Dec. 2019 through Aug. 2024 revealed complaints that were not investigated. For example:
a. Complaints received for your Gripe Water Original and Gripe Water Night Time under the category “(redacted)” revealed there were (redacted) complaints that were not investigated, (redacted) of which met the criteria for a serious adverse event.
b. Complaints received for your Gripe Water Original and Gripe Water Night Time under the category “(redacted),” “(redacted),” and “(redacted)” revealed at least (redacted) complaints that were not investigated. Of these (redacted) complaints, (redacted) were resolved as “(redacted)” with no further action documented.
In your Oct, 17, 2024, response, you committed to updating your (redacted) procedure and conducting a retrospective review of all complaints received from 2019-2024 to ensure all are fully investigated and completely documented. You also indicated that any complaints that are determined to be a serious adverse event will be reported per your revised (redacted) procedure, and that you will conduct retraining of your employees on the revised procedure, as well as perform monthly monitoring of your firm’s compliance with the revised procedure.
In your response dated Nov. 22, 2024, you provided a copy of your revised (redacted) procedure and stated that your employee retraining was completed on Nov. 20, 2024. You also indicated your retrospective review of complaints is in-progress. As your corrective actions are still in progress, we cannot evaluate the adequacy of your corrections at this time.
3. You failed to comply with the requirements for records of product complaints in 21 CFR111.570. Specifically, written records of product complaints that are related to good manufacturing practice must include the findings of the investigation and follow-up action taken when an investigation is performed [21 CFR 111.570(b)(2)(ii)(F)]. However, a review of your electronic consumer complaint records revealed your complaint records, in which your Quality Manager stated that (redacted). For example, complaint #(redacted), received Oct, 4, 2021, in which the complainant described their baby turning blue after administering Gripe Water Night Time, your electronic record indicates the quality investigation is completed. However, you were unable to provide documentation pertaining to the quality review and investigation of this complaint.
In your initial response, you committed to revising your (redacted) procedure and including a detailed template which will be designed to capture all required steps and follow-up actions for complaint investigations. You provided FDA with this revised procedure and the consumer complaint investigation form. We will evaluate the adequacy of this corrective action during our next inspection of your firm.
Failure to submit a serious adverse event report
You failed to submit a Serious Adverse Event Report (SAER) for a dietary supplement within 15 business days after receiving a report about the adverse event, as required by section 761(c) of the Act [21 U.S.C. 379aa-1(c)]. Specifically, you received reports of at least (redacted) serious adverse events between Dec. 2019 and Aug. 2024, but did not submit a SAER as required. For example, our inspection found you received reports of infants choking, infants that stopped breathing, and infants that were admitted to the hospital after being administered your Gripe Water Original products. For example:
a. On January 19, 2021, you received a complaint (#redacted)) in which the complainant described giving their two-month-old baby Gripe Water Original on Jan.12, 2021, and a second dose on Jan. 13, 2021, when they noticed he had a fever of 101.8 degrees. The complainant explained they called the local emergency room which advised the complainant to bring the baby to the hospital. The complainant explained their baby was sent to a bigger hospital where additional tests, including blood work and a spinal tap were performed and he was admitted to the hospital where he stayed until Jan. 17, 2021. Per the complainant, the tests were positive for E. coli, although the complainant reported the hospital could not tell them what caused the infection.
b. On Oct. 7, 2021, you received a complaint (#redacted) in which the complainant described their daughter was born prematurely, they used Gripe Water Original and the infant vomited and was taken to the emergency room. The complainant further explained the infant “redacted.”
c. On Oct. 15, 2021, you received a complaint (#redacted) in which the complainant described their six-week-old infant choked on Gripe Water Original. Per your complaint record, the complainant explained their infant “(redacted).” Your complaint record further explains the complainant attempted cardiopulmonary resuscitation (CPR) multiple times until the infant began breathing again. The complainant also reported that paramedics were called and looked over their infant.
d. On March 30, 2022, you received a complaint (#redacted) in which the complainant gave their baby Gripe Water Original and the baby “(redacted).” The complainant further explained they were “(redacted).”
e. On May 4, 2023, you received a complaint (#redacted) in which the complainant described giving their baby Gripe Water Original and “redacted.”
f. On July 30, 2024, you received a complaint (#redacted) in which the complainant described their child choking on Gripe Water Original on two different occasions. The complainant explained they gave their two-month-old some Gripe Water Original, “(redacted).”
Under section 761(c) of the Act, you must submit a report of a serious adverse event associated with any of your dietary supplements no later than 15 business days after a report of the event is received through the address or phone number provided on your dietary supplement products.
Because prompt submission of such serious adverse event reports is important for public health reasons, the agency recommends that all serious adverse events be reported to FDA within 15 business days of receipt regardless of the means by which you receive the initial report. These serious adverse event reports should be submitted under the MedWatch Form 3500A. More information on adverse event reporting can be found on FDA’s website at www.fda.gov, in the publication “Questions and Answers Regarding Adverse Event Reporting and Recordkeeping for Dietary Supplements as required by the Dietary Supplement and Nonprescription Drug Consumer Protection Act.”
In your written response letters, with respect to the observation relating to serious adverse event reporting, you provided a revised (redacted) procedure and complaint investigation form that appear to provide adequate details for assessing the severity of the adverse events. You also committed to conducting a retrospective review of the (redacted) complaints identified during our inspection as reportable events using your revised (b)(4) procedure and reporting any complaints that are deemed reportable.
In your Oct.17, 2024, response, you quote from the guidance “Questions and Answers Regarding Adverse Event Reporting and Recordkeeping for Dietary Supplements as required by the Dietary Supplement and Nonprescription Drug Consumer Protection Act” and explain that you interpreted the FDA guidance as stating the details of the event come from the perspective of trained health care professionals. However, FDA’s guidance clearly states, as quoted in your response, “[W]e encourage responsible persons to use trained health care practitioners to elicit information from reporters, computer-assisted interview technology, targeted questionnaires, and/or other appropriate methods that help focus the line of questioning.” It does not appear that your firm was using either trained healthcare professionals, computer-assisted interview technology, targeted questionnaires, or other methods that would help focus the line of questioning; your (redacted) procedure required customer service representatives to determine whether a complaint required escalation as an adverse event or serious adverse event. It is not a requirement that the details of events come from trained healthcare professionals; it does not require “(redacted)” as stated in your response. In fact, the guidance defines an initial reporter as the person who first notifies the responsible person about the serious adverse event and “can be the patient, a family member, or some other person (e.g., doctor, pharmacist).”
According to your Nov. 22, 2024, response, as a result of your retrospective review of the complaints identified during our inspection, you are in the process of reporting (redacted) of the complaints to FDA as SAERs, and are re-opening the remaining complaints for one year in order to try and gather additional information needed for reporting the SAERs. Per your response, you have concluded these remaining complaints are also qualifying events per your procedure, but do not have complete data elements.
Of the remaining complaints that you identified as qualifying events, the missing data element for many of these complaints is listed as “(redacted.” However, per the complaint records reviewed during our inspection, the product name is identified as Gripe Water Original for each of these complaints. It is unclear why the complaint records reviewed during our inspection identified the product as “Gripe Water Original” for each of these complaints, but your retrospective review has now determined the complainant didn’t specify the product.
Misbranded Ddetary supplements
1. Your Gripe Water, Gripe Water Night Time, and Kids Cough Syrup & Mucus Day + Night Combo Pack products are misbranded within the meaning of section 403(q)(5)(F) [21 U.S.C. 343(q)(5)(F)] in that the presentation of the nutrition information on the labeling of your products does not comply with 21 CFR 101.9, 21 CFR 101.36, and 21 CFR 101.2. For example:
a. The product’s inner bottle labels do not bear nutrition information, as required by 21 CFR 101.36. The unit container is exempted from these requirements if the unit container bears the statement “This Unit Not Labeled for Retail Sale” [21 CFR 1.24(a)(24)].
b. The dosage guide and/or directions for use are placed above the Supplement Facts label, which is not in accordance with 21 CFR 101.2(a) and (e). Nutrition information should appear on the principal display panel (PDP) or directly to the right of the PDP with no intervening material in between.
c. For your Gripe Water Night Time and Kids Cough Syrup & Mucus Day + Night Combo Pack, the serving size in the Supplement Facts labels fails to be declared as required by 21 CFR 101.36(b)(1)(i). Serving size must be expressed in common household measures as set forth in 21 CFR 101.9(b) and must be followed by the equivalent metric quantity in parenthesis (fluids in milliliters and all other foods in grams).
Unapproved new drug
FDA reviewed your website at the internet address www.mommysbliss.com in December 2024 and determined that you take orders there for your Gripe Water Original. The claims on your website establish that your product Gripe Water Original is a drug under section 201(g)(1)(B) of the Act [21 U.S.C. 321(g)(1)(B)] because it is intended for use in the cure, mitigation, treatment, or prevention of disease. As explained further below, introducing or delivering this product for introduction into interstate commerce for such uses violates the Act. Thus, in addition to being an adulterated and misbranded dietary supplement, your Gripe Water Original is also an unapproved new drug under section 201(g)(1)(B) of the Act [21 U.S.C. 321(g)(1)(B)].
Examples of some of the claims that provide evidence that your Gripe Water Original product is intended for use as a drug include:
From the blog post on your website: Acid Reflux = The Pits – Mommy’s Bliss
• “Acid reflux, also known as gastroesophageal reflux or GER, is when acids and content of the stomach come back up into the baby’s esophagus. It happens because the lower esophageal sphincter isn’t fully developed. . . .[I]f [a baby’s esophageal sphincter] fails to develop correctly or becomes weak, a baby may develop GERD (gastroesophageal reflux disease) which has more severe complications. . . .
How do you know if your baby has acid reflux?
The symptoms of acid reflux are typically clear and easy to read….
1. Frequent Vomiting….2. Irritability….The acid of the digestive juices irritates the stomach and esophagus….3. Persistent Coughing or Wheezing….There is a link between acid reflux, wheezing, coughing, and even asthma….5. Colic The persistent crying of a colicky baby could be a symptom of reflux. The irritation of the stomach and the esophagus from all those digestive juices may trigger your baby into colic….How do you help a baby with acid reflux?….
Try Gripe Water
Gripe water can also be a great way to ease symptoms of acid reflux in infants. It is a natural approach to help reduce the stomach acid that causes pain. . . .
Mommy’s Bliss Gripe Water is a safe and gentle way to help ease your baby’s stomach discomfort. The organic ginger and fennel relieve the irritation and prevent the stomach acid from flowing up into the esophagus. Fennel is known for its ability to reduce inflammation and acid in the stomach while ginger’s phenolic compounds help relieve irritation and reduce gastric contractions.”
Additionally, your blog post titled “Acid Reflux = The Pits,” in discussing the “link between acid reflex, wheezing, and coughing,” links to an article from the Mayo Clinic article entitled “Asthma and acid reflux: Are they linked?” (Asthma and acid reflux: Are they linked? – Mayo Clinic). This link from your blog further suggests that your Mommy’s Bliss Gripe Water Original is intended for the cure, mitigation, treatment, or prevention of GERD and asthma.
Your product is not generally recognized as safe and effective for the above referenced uses and, therefore, the product is a “new drug” under section 201(p) of the Act [21 U.S.C. 321(p)]. With certain exceptions not applicable here, new drugs may not be legally introduced or delivered for introduction into interstate commerce without prior approval from FDA, as described in sections 301(d) and 505(a) of the Act [21 U.S.C. 331(d), 355(a)]. FDA approves a new drug on the basis of scientific data and information demonstrating that the drug is safe and effective.
Misbranded drug
A drug is misbranded under section 502(f)(1) of the Act [21 U.S.C. 352(f)(1)] if the drug fails to bear adequate directions for its intended use(s). “Adequate directions for use” means directions under which a layperson can use a drug safety and for the purposes for which it is intended (21 CFR 201.5). Prescription drugs, as defined in section 503(b)(1)(A) of the Act [21 U.S.C. 353(b)(1)(A)], can only be used safely at the direction, and under the supervision, of a licensed practitioner.
Your Gripe Water Original is intended for treatment or prevention of one or more diseases that are not amenable to self-diagnosis or treatment without the supervision of a licensed practitioner. Therefore, it is impossible to write adequate directions for a layperson to use your product safely for its intended purpose. Accordingly, Gripe Water Original fails to bear adequate directions for its intended use and, therefore, the product is misbranded under section 502(f)(1) of the Act [21 U.S.C. 352(f)(1)]. The introduction or delivery for introduction into interstate commerce of this misbranded drug violates section 301(a) of the Act [21 U.S.C. 331(a)].
++++++++++++++++++++++++++++++++++++++++++++++++++++++++++++++
Marin Baking LLC
1512 4th Street
San Rafael, CA 94901
The United States Food and Drug Administration (FDA) inspected your ready-to-eat (RTE) bread product manufacturing facility, located at 1512 4th Street, San Rafael, CA, from Nov. 14 through Nov. 26, 2024. During our inspection of your facility, FDA investigators found significant violations of the Current Good Manufacturing Practice, Hazard Analysis, and Risk-Based Preventive Controls for Human Food regulation (CGMP & PC rule), Title 21, Code of Federal Regulations, Part 117 (21 CFR Part 117). During the inspection, FDA collected filth samples from various areas within your manufacturing facility, and the analytical results revealed rodent excreta pellets and multi-stage beetles (adult and larva).
Based on FDA’s inspectional and analytical findings, we have determined the RTE bread products processed in your facility are adulterated within the meaning of section 402(a)(4) of the Federal Food, Drug, and Cosmetic Act (the Act) [21 U.S.C. § 342(a)(4)], in that they were prepared, packed or held under insanitary conditions whereby they may have become contaminated with filth, or whereby they may have been rendered injurious to health. In addition, failure of the owner, operator, or agent in charge of a covered facility to comply with the preventive controls provisions of the CGMP & PC rule (located in Subparts A, C, D, E, F, and G of Part 117) is prohibited by section 301(uu) of the Act [21 U.S.C. § 331(uu)].
At the conclusion of the inspection, the FDA investigators issued an FDA Form 483 (FDA 483), Inspectional Observations. We received your written response, dated Dec. 12, 2024, describing corrective actions planned by your facility. After reviewing the inspectional findings and response that your firm provided, we are issuing this letter to advise you of FDA’s concerns and provide detailed information describing the findings at your facility. We address your response below.
Hazard Analysis and Risk-Based Preventive Controls (21 CFR Part 117, Subpart C):
1. Your written allergen preventive controls did not include procedures, practices, and processes for ensuring protection of food from allergen cross-contact, including during storage, handling, and use; and for food labeling to ensure the food is not misbranded under section 403(w) of the Act, as required by 21 CFR 117.135(c)(2). Specifically:
a. Your facility’s written hazard analysis determined that “allergens” are a hazard requiring a preventive control at the (redacted) steps for “All Dough Types” (in-process food) and at the (redacted) steps for “All Bread Types” (finished product). Your facility manufactures a variety of bread products with unique allergens (such as sesame) on shared food-contact equipment and on the same production day. Your Food Safety Plan document indicates that the hazard of allergen cross-contact will be significantly minimized or prevented through employee hygiene practices and cleaning/sanitizing of “work surfaces” such as tables, mixers, divider/molder, and pans/racks. However, the “SANITATION PREVENTIVE CONTROLS” section of your Food Safety Plan did not address control of allergen cross-contact for shared food-contact equipment at the (redacted) step for the finished product. Furthermore, your written corrective action procedures for your allergen controls did not include steps to evaluate all affected food for safety and prevent all affected food from entering commerce if you cannot ensure food is not adulterated (see 21 CFR 117.150(a)(2)).
In addition, your sanitation procedures were not completely followed. Your “SANITATION PREVENTIVE CONTROLS” section of your Food Safety Plan for the (redacted) steps indicates regular cleaning and sanitizing of “(redacted)” will occur between “(redacted).” However, sanitation only occurs once (redacted) day at the end of production and not all shared food-contact equipment is included in your daily sanitation. For example, your wire racks used for (redacted) are cleaned every (redacted) months. In addition, the list of equipment in your “SANITATION SCHEDULE” document does not include all shared food-contact equipment. For example, (redacted).
We note that you did not have adequate controls in place for allergen cross-contact, as evidenced by the following observations during the inspection on November 19, 2024:
i. Sesame seeds were observed on the food-contact surfaces of baking trays holding exposed Sweet Longie bread, which does not contain sesame seeds as an ingredient. In addition, at least two loaves of the Sweet Longie bread appeared to have sesame seeds baked onto the outer surface of the loaf.
ii. Sesame seeds were observed on the food-contact surfaces of baking trays holding exposed Ciabatta bread, which does not contain sesame seeds as an ingredient. In addition, at least one roll of Ciabatta bread appeared to have sesame seeds baked onto the outer surface of the roll.
Your facility placed the Sweet Longie and Ciabatta breads exposed to sesame seeds into food waste containers for disposal on November 19, 2024.
Your response indicated you will develop “(redacted)”; implement monitoring, verification, and corrective actions; “(redacted)”; maintain “(redacted)”; and use a (redacted) system to “(redacted).” However, we cannot assess the adequacy of your stated corrective actions because you have not provided supporting documentation, such as sanitation procedures and implementation records.
b. Your facility’s written hazard analysis determined that “allergens” are a hazard requiring a preventive control at the (redacted) step for “(redacted)” (finished product). Your facility manufactures a variety of RTE bread products that contain allergens (such as wheat, milk, and sesame). Your “FOOD ALLERGEN PREVENTIVE CONTROLS” section of your Food Safety Plan states, “(redacted).” However, your “FOOD ALLERGEN PREVENTIVE CONTROLS” later indicates these procedures are only required at the (redacted) step for raw materials to “(redacted)” (e.g., “(redacted)”). Although your procedures address labelling of ingredient storage bins, your allergen controls did not include procedures to properly identify undeclared allergens and ensure the correct label is applied to the correct finished product. Your RTE breads are packaged in clear plastic bags, and you did not have procedures in place to ensure labels are affixed to the packaging with the correct major food allergens stated. Therefore, your Food Safety Plan did not include preventive controls to ensure that all food allergens are included on the finished product label (see 21 CFR 117.135(c)(2)(ii)).
We note that you did not have adequate controls in place for undeclared allergens. We observed during our inspection that most of your bread products (such as Sesame Seeded Hot Dog Rolls) are packaged in unlabeled plastic bags and then the bags are placed into unlabeled cardboard cases or on plastic bakery trays for distribution.
Your response indicated you will establish “(redacted)” and regularly audit “(redacted).” However, we cannot assess the adequacy of your stated corrective actions because you have not provided supporting documentation, such as labeling procedures and implementation records.
2. You did not identify and evaluate a known or reasonably foreseeable hazard to determine whether it required a preventive control for your RTE bread products, as required by 21 CFR 117.130(a)(1). Specifically, your facility’s written hazard analysis did not consider recontamination with environmental pathogens, such as Salmonella, at all steps where your RTE bread products are exposed to the environment. Though your hazard analysis determined that “(redacted)” are a hazard requiring a preventive control at the (redacted) steps for “(redacted)” (finished product), it did not consider recontamination with environmental pathogens, such as Salmonella, as a known or reasonably foreseeable hazard at the (redacted) step. Your facility manufactures RTE bread products (such as RTE Sliced Sourdough bread) which are exposed to the environment after baking and handled by employees prior to being packaged, such as during the (redacted) step. The packaged food does not receive any further lethal treatment or otherwise include a control measure (such as a formulation lethal to the pathogen) that would significantly minimize pathogens. Therefore, contamination with environmental pathogens is a known or reasonably foreseeable hazard.
Furthermore, environmental monitoring is required if contamination of an RTE food with an environmental pathogen is a hazard requiring a preventive control (see 21 CFR 117.165(a)(3)). You were not performing environmental monitoring to evaluate the effectiveness of your sanitation practices.
In addition, you did not follow your (redacted) sanitation procedures. Your “SANITATION PREVENTIVE CONTROLS” section of your Food Safety Plan indicates (edredact).” Your verification procedure states that the “(redacted).” However:
i. Your facility’s General Manager indicated that food-contact surfaces on the large and small slicer are not sanitized. Your “SANITATION SCHEDULE” indicates (redacted).
ii. Your facility’s General Manager indicated that wire racks are cleaned with water and detergent every (redacted) months and the tables are wiped down daily with a cloth, but these food-contact surfaces are not sanitized. Additionally, frequency of cleaning for your tables and wire racks was missing from your “SANITATION SCHEDULE.”
iii. You manufacture (redacted) days per week and your “SANITATION SCHEDULE” indicates equipment (e.g., (redacted) are cleaned/sanitized (redacted) days per week. However, your employee responsible for monitoring the sanitation process is only present at the facility (redacted) days per week. Therefore, monitoring is not performed (redacted) out of the (redacted manufacturing days at your facility each week.
Furthermore, preventive controls are subject to preventive control management components (monitoring, verification, and corrective actions) as appropriate to ensure the effectiveness of the preventive controls, taking into account the nature of the preventive control and its role in the facility’s food safety system (see 21 CFR 117.140). We note that you did not have adequate controls in place for contamination with environmental pathogens regarding sanitation, monitoring, and verification activities, as evidenced by the following observations during the inspection on November 19, 2024:
i. Your large slicer was observed to have an accumulation of apparent caked-on food residue or debris on multiple food-contact surfaces prior to and during use for slicing of RTE Sliced Sourdough bread.
ii. Your small slicer was observed to have an accumulation of apparent caked-on food residue or debris on food-contact surfaces on the inside of the slicer prior to use for cutting RTE Sesame Seeded Hot Dog Rolls.
iii. Your wire racks holding RTE bread, such as Sourdough and Whole Wheat loaves, were observed to have an accumulation of apparent caked-on food residue or debris on the food-contact surfaces.
Your response indicated you will develop “(redacted)”; implement monitoring, verification, and corrective actions; “(redacted)”; maintain “(redacted)”; and establish environmental monitoring. However, we cannot assess the adequacy of your stated corrective actions because you have not provided documentation, such as your sanitation procedures and monitoring records. We will assess the adequacy and implementation of your corrective actions during a future inspection.
Current Good Manufacturing Practice Requirements (21 CFR Part 117, Subpart B):
1. You did not clean your non-food-contact surfaces of equipment used in the operation of a food plant in a manner and as frequently as necessary to protect against contamination of food, food-contact surfaces and food packaging materials, as required per 21 CFR 117.35(e). Specifically, on November 20, 2024, a dark-colored buildup of apparent filth was observed directly above ice on the interior of your ice machine. Ice from this ice machine is used in the production of dough such as for the RTE Sourdough Longie bread.
2. You did not take effective measures to exclude pests from the manufacturing, processing, packing, and holding areas and to protect against the contamination of food on the premises by pests, as required by 21 CFR 117.35(c). Specifically:
a. Rodent activity:
i. On November 19, 2024, too numerous to count rodent excreta pellets (REPs) were observed on a dry ingredient storage shelf located against a wall in the cooling and packaging area of the production facility. This storage shelf contained bags of dry ingredients (such as sesame seeds, calcium propionate, rolled oats, and corn meal) and (redacted) bags were observed to have apparent rodent gnaw holes. RTE loaves of Sourdough bread were cooling on a rack approximately (redacted) from this dry ingredient storage shelf.
ii. On Nov. 19, 2024, 1 REP was observed on the floor adjacent to the three-compartment sink located in the mixing room, and 1 REP was observed on the floor underneath the same three-compartment sink. Dutch Crunch dough was glazed approximately (redacted) feet from this three-compartment sink.
iii. On Nov. 19, 2024, 1 REP was observed on the floor along the (redacted) facing wall of the production facility. Containers used to hold food waste were located approximately (redacted) feet from where the REP was observed.
iv. On Nov. 19, 2024, 2 REPs were observed on top of cardboard boxes holding plastic bags used to package RTE “SOUR SLICED FRENCH” and RTE “EUROPEAN STYLE WHEAT” bread. These boxes were stored against the wall behind ovens (redacted), which was approximately (redacted) feet from the slicing machine where an employee was slicing RTE Sourdough bread.
v. On Nov. 20, 2024, 1 REP was observed on the floor in the mixing room approximately (redacted) inches away from the Erika Record Rounder and approximately (redacted) inches from the wooden tabletop used during production.
vi. On Nov. 20, 2024, 2 REPs were observed on the floor next to the walkway leading down to the flour silo and approximately (redacted) inches from a metal shelf holding brown paper bags.
vii. On Nov. 20, 2024, 1 REP was observed on a cardboard surface approximately (redacted) feet from the flour silo.
viii. On Nov. 20, 2024, 1 REP was observed on the floor approximately (redacted) feet from an ice machine containing ice used in the production of dough such as for the RTE Sourdough Longie bread.
b. Insect activity:
i. On Nov. 19, 2024, 1 dead insect was observed in the mixing room on top of a stainless-steel table used to measure ingredients such as butter flavor. A container of butter flavor ingredient was located approximately (redacted) feet away.
ii. On Nov. 19, 2024, 1 dead insect was observed in the mixing room on the floor adjacent to the three-compartment sink. Dutch Crunch dough was glazed approximately (redacted feet from this three-compartment sink.
iii. On Nov. 20, 2024, 1 live insect larva was observed in the mixing room inside an electrical panel on the back of an unused mixer. This mixer was approximately (redacted) feet from a wooden tabletop used during production.
iv. On Nov. 20, 2024, 1 live insect was observed on a blue plastic bag located approximately (redacted) from the flour silo.
c. FDA collected several samples for filth during our inspection from within your manufacturing facility locations noted above (samples 1277727 and 1277728). These samples were submitted to FDA labs for analysis. These samples resulted in numerous filth findings including the presence of rodent excreta pellets of a size implicating rat or mouse excreta pellets and multi-stage beetles (adult and larvae). The filth samples further demonstrate the presence of rodents and insect activity throughout the facility through the presence of rodent hairs and in pellet morphology as well as confirmation of various species of insects at larval and adult stages.
d. On Nov. 14, 2024, a gap of approximately (redacted) was observed below the (redacted emergency exit door.
e. During the inspection, your (redacted) door into the cooling and packaging area was observed to be left open at multiple points throughout the day.
Your facility placed the bags of dry ingredients with apparent rodent gnaw holes into food waste containers for disposal on November 19, 2024.
Your response indicated you (redacted). However, we cannot assess the adequacy of your stated corrective actions because you have not provided documentation, such as your pest control records, showing implementation of the proposed corrective actions. We will assess the adequacy and implementation of your corrective actions during a future inspection.
In addition to the violations described above, we offer the following comment:
- We note that each individual engaged in manufacturing, processing, packing, or holding food (including temporary and seasonal personnel) or in the supervision thereof must receive training in the principles of food hygiene and food safety, including the importance of employee health and personal hygiene, as appropriate to the food, the facility, and the individual’s assigned duties, as required by 21 CFR 117.4(b)(2). You are required to establish and maintain documentation of this training for each individual, as provided by 21 CFR 117.4(d).
(To sign up for a free subscription to Food Safety News, click here)
Source: https://www.foodsafetynews.com/2025/07/fda-warns-manufactures-of-infant-drugs-and-bread-products-about-violations/
Anyone can join.
Anyone can contribute.
Anyone can become informed about their world.
"United We Stand" Click Here To Create Your Personal Citizen Journalist Account Today, Be Sure To Invite Your Friends.
Before It’s News® is a community of individuals who report on what’s going on around them, from all around the world. Anyone can join. Anyone can contribute. Anyone can become informed about their world. "United We Stand" Click Here To Create Your Personal Citizen Journalist Account Today, Be Sure To Invite Your Friends.
LION'S MANE PRODUCT
Try Our Lion’s Mane WHOLE MIND Nootropic Blend 60 Capsules
Mushrooms are having a moment. One fabulous fungus in particular, lion’s mane, may help improve memory, depression and anxiety symptoms. They are also an excellent source of nutrients that show promise as a therapy for dementia, and other neurodegenerative diseases. If you’re living with anxiety or depression, you may be curious about all the therapy options out there — including the natural ones.Our Lion’s Mane WHOLE MIND Nootropic Blend has been formulated to utilize the potency of Lion’s mane but also include the benefits of four other Highly Beneficial Mushrooms. Synergistically, they work together to Build your health through improving cognitive function and immunity regardless of your age. Our Nootropic not only improves your Cognitive Function and Activates your Immune System, but it benefits growth of Essential Gut Flora, further enhancing your Vitality.
Our Formula includes: Lion’s Mane Mushrooms which Increase Brain Power through nerve growth, lessen anxiety, reduce depression, and improve concentration. Its an excellent adaptogen, promotes sleep and improves immunity. Shiitake Mushrooms which Fight cancer cells and infectious disease, boost the immune system, promotes brain function, and serves as a source of B vitamins. Maitake Mushrooms which regulate blood sugar levels of diabetics, reduce hypertension and boosts the immune system. Reishi Mushrooms which Fight inflammation, liver disease, fatigue, tumor growth and cancer. They Improve skin disorders and soothes digestive problems, stomach ulcers and leaky gut syndrome. Chaga Mushrooms which have anti-aging effects, boost immune function, improve stamina and athletic performance, even act as a natural aphrodisiac, fighting diabetes and improving liver function. Try Our Lion’s Mane WHOLE MIND Nootropic Blend 60 Capsules Today. Be 100% Satisfied or Receive a Full Money Back Guarantee. Order Yours Today by Following This Link.
